About PVDF and History
PVDF is the four-letter acronym for Polyvinylidene Fluoride, one of the world’s toughest, most used high purity, synthetic materials. PVDF is widely acclaimed and chosen for applications due to its enhanced resistance profile, mechanical and thermal strength, magno-electric properties as well as its ability for use as a solid and in liquid coating forms. Initially produced in 1969, polyvinylidene fluoride is also known as polyvinylidene difluoride, PVF2, and by its popular trade name Kynar®. PVDF is a polymer that belongs to the thermoplastic category of plastics. Polymers by definition, and thus many plastics, are long chains of repeating molecule units that have been linked together through a human-derived synthesis reaction.
Polyvinylidene fluoride is defined as a semi-crystalline fluoropolymer due to the presence of elemental fluorine (F) within the starting molecule base used to make PVDF. The presence of fluorine within PVDF and its fairly 50 / 50 amorphous / crystalline structure contributes to this unique plastic’s well-known superior service and tolerance ranges. PVDF is both known and implemented for its increased resilience against many of the chemical, biological, and mechanical stresses that similar and similarly used structural materials often encounter.
Compared to other plastics, plastic grades, metals and their alloys, PVDF is considered to be on par or far surpass these materials’ range of operation and acceptability for use. Although no material is indefinitely stable or inert to everything, and true suitability is defined by the fine details of the application, PVDF carries an excellent cost to performance ratio that is owed to its superior resistance, durability and compatibility profile.
How is PVDF Made
PVDF is initially produced as a raw resin that results from the chemical synthesis reaction known as polymerization. Polymerization is used to produce the various materials collectively known as plastics, such as polyethylene, PVC and polypropylene. The polymerization of plastic products such as PVDF often differ in their required production parameters, their operating catalyst and most importantly, the starting base molecule, i.e. monomer. In PVDF, the monomer vinylidene fluoride (abbr. VDF; also known as: 1, 1-difluoroethylene) is polymerized. This means the single VDF units are joined end-to-end to formulate a long network molecule known as a polymer -- a plastic -- and here polyvinylidene fluoride -- PVDF, Kynar.
In PVDF, the base starting material, VDF, is the reactive result of further chemical processing of byproduct materials from refining natural oils and flammable gases. To fabricate PVDF, VDF is subjected to free radical polymerization that occurs when heated to temperatures up to 300°F (150°C) and pressures up to 300 atm (30,400 kPA; 4400 psi). Polymerized PVDF is a resin type material that can be manipulated similar to other types of plastic resins. Molten PVDF resins can be machined, extruded or molded via injection, rotation, transfer or compression methods to form a near indefinite range of possible PVDF products in the form of sheets, films, pipes, containers, specialized equipment and individual items, parts or components.
PVDF Properties and Characteristics
Polyvinylidene fluoride is a high weight fluoropolymer and durable thermoplastic with excellent thermal, mechanical, electrical, and chemical characteristics. These properties make PVDF extremely well suited for material engineering and plastic type applications. Kynar PVDF is largely inert, resilient and stable for long term service. As a thermoplastic material, PVDF loses its rigidity as heated, which allows for product recycling and reformation. As a synthetic plastic, Kynar provides resistant service in high temperature environments, harsh / aggressive chemical handling, pressurized fluid systems and outdoor installations. PVDF products are approved for use up to 284°F temperature maximums prior to material softening. This is much higher than PVC or CPVC with service temperatures that max out at 140°F and 200°F, respectively. Resins of PVDF can be acceptable for even greater temperatures depending on the detailed grade specifics.
Products made from PVDF are inherently resistant to many troublesome effects common to other materials. PVDF is resistant to surface abrasion, to the growth of fungi, algae and microbial films, to the development of fire and smoke, to damage from ozone exposure and use, and is naturally unaffected by the degradation effects of sunlight UV that most other plastics are susceptible. PVDF is a strong insulator and resists hot/cold thermal transfer and electrical conductance. Molecularly, PVDF also expresses unique piezoelectric properties, meaning it is capable of responding to and influencing electrical and/or magnetic fields.
Chemically, PVDF ranks high among synthetic and metallic materials for its general compatibility as well as its resistance to chemical permeation and attack. PVDF is considered chemically stable with excellent resistance against: strong acids, strong oxidants, solvents, halogens, alcohols, salts and weak bases. PVDF is reported as being potentially susceptible and may experience softening and/or swelling on exposure to strong bases, esters and ketone defined chemicals.
How is PVDF Commonly Used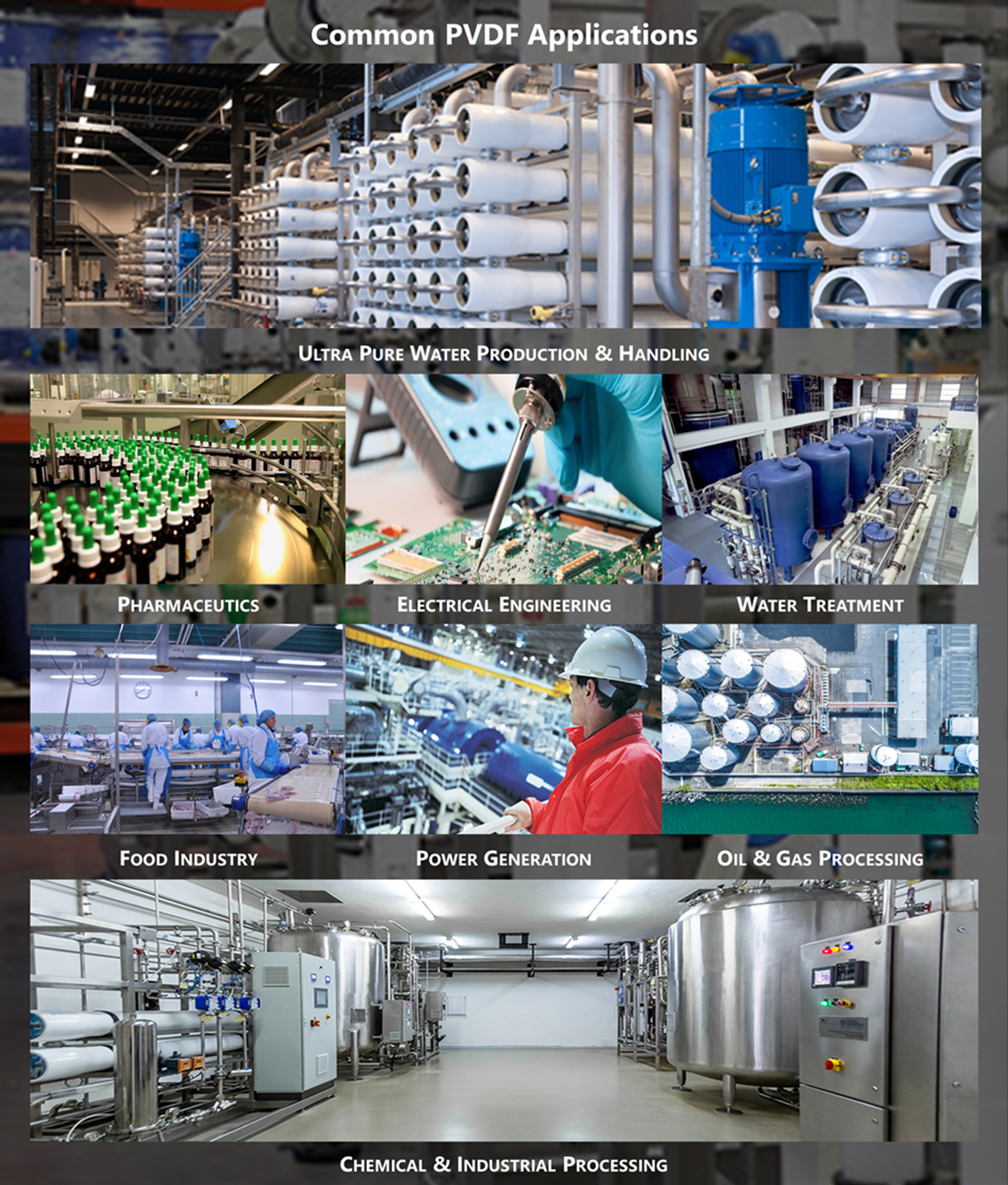
Due to PVDF’s versatile strengths and increased range of operational parameters, the synthetic plastic is frequently selected for use and across a diverse cloud of applications. Its thermal tolerance and insulation capabilities contribute to PVDF’s use as plumbing for product synthesis reactions, energy production reactors, electrical cable coatings and wiring. The chemical tolerance and low permeation of PVDF contributes to its use in the chemical process industry. PVDF is often used for handling harsh and unique liquids to gaseous products that can include sulfuric, nitric and hydrochloric acid, compounds such as halogenated, aliphatic and aromatic solvents as well as natural and refined products, oils and combustible fuels. Its high abrasion resistance and purity profile contributes to PVDF’s use in pharmacology and healthcare settings and their equipment, the production and use of ultrapure water, and for the repeated long term contact with consumables in food grade applications. These properties also make PVDF effective for use in purification membranes employed in water filtration and wastewater treatment.
Kynar PVDF is often used in various plumbing scenarios due to its high/low temperature tolerances, non toxic status, and resistance to ultraviolet effects, nuclear radiation and microbiological growth. As plumbing, PVDF is also frequent in plenum applications due to meeting 25/50 flame, smoke spread ratings for ASTM standards. Additional PVDF scenario industry application and uses include: within piezoelectric devices, transducers and computerized components; as an additive within paints; as a weather-protectant in coatings for roofs and equipment, and; in the production of lithium ion batteries, cathodes and anodes. In list form, common uses for PVDF include: plumbing, pipes and tubing; structural equipment and construction materials; electrical engineering; power plant operation; chemical material handling and productions; pharmaceutics, health, high purity and food grade scenarios.
What is PVDF Takeaways
PVDF -- polyvinylidene fluoride or Kynar -- is a stable, largely non reactive, semi crystalline fluoropolymer. This synthetic plastic is often considered superior to comparative materials: PVC, polyethylene, and even steel to stainless steel. PVDF has heightened durability against chemical corrosion, absorption, weathering and degradation that promotes its use across industries and sectors of society, commerce and manufacturing. As a plastic, PVDF is capable of extensive manipulation, fabrication and product inclusion, from cable insulators and structural coatings to nuclear reactor equipment and water filtration membranes. If considering PVDF for an application, know that it will likely make a more-than-excellent option, but as with any intricate use or chemical / physical scenario, always verify compatibility prior to use. If you have further questions, comments or are looking for PVDF plumbing, pipes and fittings, reach out to our professional experts today to assist you with any and all your PVDF needs.